Two-day SIAM Hackathon at CSE23 Explores Critical Problems in Industry
The 2023 SIAM Conference on Computational Science and Engineering (CSE23), which took place from February 26 to March 3, ventured outside of the U.S. for the first time and made its way to Amsterdam, the Netherlands. With more than 2,000 attendees, the meeting marked the largest gathering of mathematicians in the Netherlands to date. It also introduced an exciting special event: the first-ever SIAM Hackathon.
The hackathon was held on February 25 and 26 (just before CSE23) in the Van der Valk Hotel Amsterdam, which was close to the CSE23 venue (though participation in the hackathon was independent from participation in the conference). Wolfgang Bangerth (Colorado State University), David Gleich (Purdue University), Dirk Hartmann (Siemens Digital Industries Software), Jeffrey Sachs (Merck), and Jesse van Doren, (Hackathon Op Maat) comprised the Organizing Committee. During the two-round, team-based competition, approximately 150 participants from all over the world tackled a wide variety of industry-based challenges that were provided by six contributing companies: Advanced Micro Devices (AMD), Advanced Semiconductor Materials Lithography (ASML), Amazon Web Services (AWS), KUKA, Institut Roche, and Siemens.
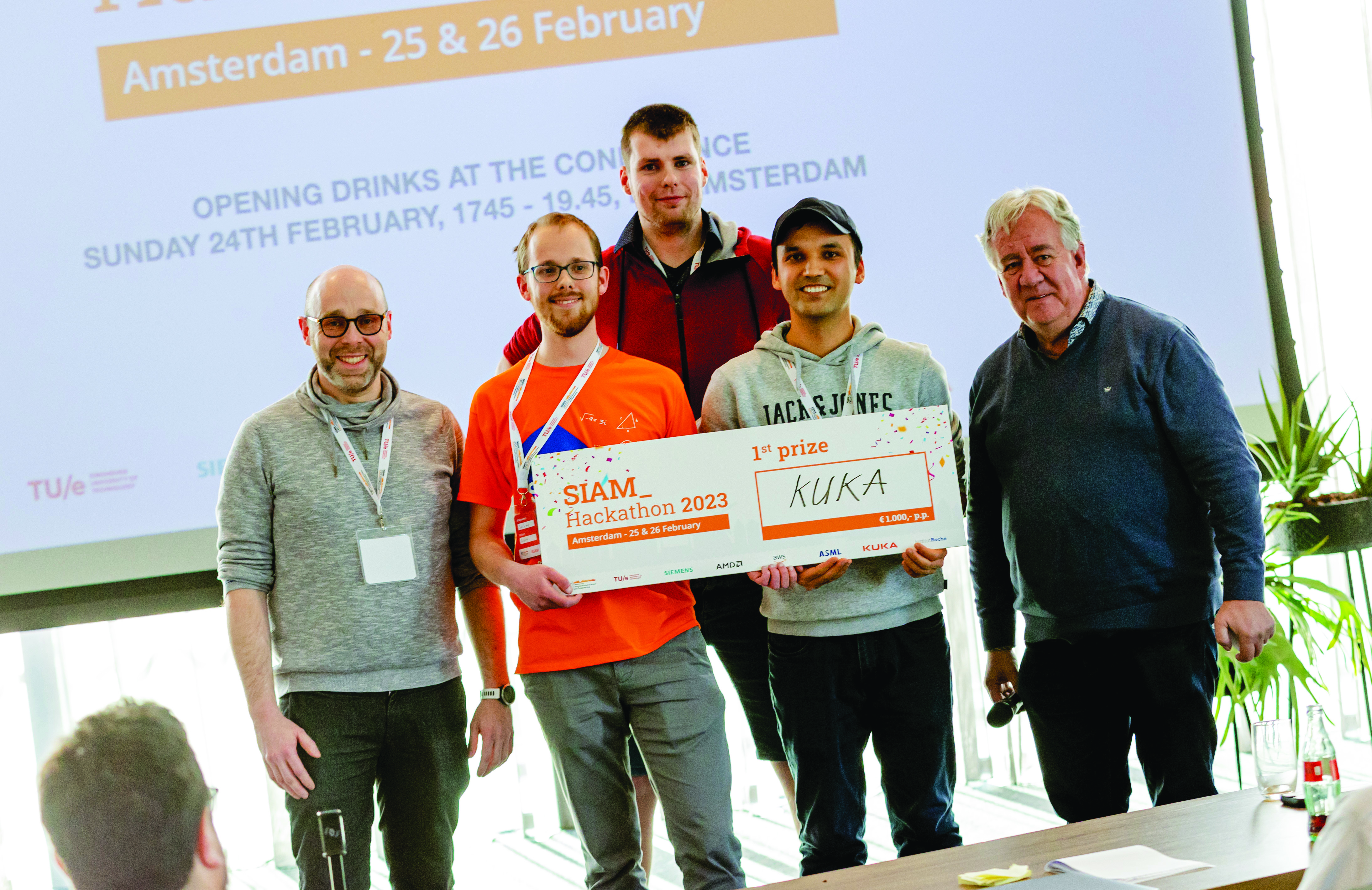
In the first round, teams of up to five individuals each worked on one of the challenges and competed with one another to advance to the second round. The six winning teams from the initial round (one for each company’s proposed problem) then vied for the first-place spot.
Each company submitted a challenge that was specific to its operations, required limited prerequisite knowledge, and was solvable with only a laptop. These problems varied in both research area and application. AMD sought a fast surrogate model for the wave equation, while ASML wanted a better model or algorithm for the accurate estimation of heat transfer between the hydrogen buffer gas and the surrounding components or boundaries of their new Extreme Ultra Violette lithography machine. AWS requested a way to stream high-fidelity simulation data over bandwidth-limited channels to consumer-grade hardware, and KUKA desired a novel strategy that would solve their warehouse optimization difficulties. Institut Roche asked teams to create a procedure that anonymizes clinical data and minimizes the introduced noise to prevent the destruction of clinically relevant trends or patterns. Finally, Siemens hoped to improve building efficiency while ensuring occupant comfort, with the ultimate goal of reducing investments and operational costs while minimizing carbon footprints.
The use of existing real-world scenarios during the hackathon allowed participants to become more familiar with potential employers, learn about the types of problems that large companies face on an everyday basis, and network with both company representatives and other attendees. At the same time, the organizations in question were able to advertise themselves and showcase the challenges that their employees are actively attempting to solve.
Individuals who signed up for the SIAM Hackathon received a description of the six challenges in advance and had to select their top three options. The organizers then evenly distributed the competitors based on their preferences. At the beginning of the first day, participants who were assigned to the same problem sorted themselves into teams; at least five groups worked on each challenge. To help create teams of people with complementary work styles and skillsets, everyone completed several tests that assigned them a classification based on their self-evaluation. The organizers encouraged individuals to collaborate with people who had different classifications to ensure diversity and balance in each group.
The newly formed teams then received more details about their respective challenges and immediately got to work. They had just over 24 hours to put together a cohesive solution and prepare a five-minute pitch. Various activities throughout the event’s duration—including a Mario Kart competition, Nerf gun fights, cardio sessions, virtual reality ping-pong, and even an opportunity to make music by poking electrodes into fruits—helped promote camaraderie and alleviate stress. Two buffet lunches and a dinner kept everyone well fed, and participants were free to return to their hotel rooms to sleep if they wished (onsite bean bag chairs also provided a comfortable setting for the occasional power nap).
After the initial 24-hour period, each group pitched their solution to the other teams who had tackled the same challenge. Representatives of the partner companies that supplied the problems judged the pitches based on a predetermined set of criteria, and the teams with the best solutions for each individual challenge won the first round. These six finalist teams had just 15 minutes to prepare and adapt their previous presentation into a new pitch for the second round of the competition. They delivered these updated pitches to all attendees—not just those who were involved with their respective challenge—which meant that they had to clearly explain the initial concept of their task as well.
The company representatives judged the second round of pitches and asked questions after each presentation. Though there were no specific guidelines for evaluation, they were not allowed to vote for the winner of their own challenge. Once all of the pitches were complete, the judges retreated for a short deliberation and announced the overall winning team.
Our team, which we dubbed “Robo Go’round,” was assigned to the KUKA challenge about cross-vehicle route planning in a warehouse. In addition to myself (a Ph.D. candidate at the University of Twente in the Netherlands), the team consisted of Wouter van Harten (a Ph.D. candidate at Radboud University in the Netherlands) and Ikrom Akramov (a Ph.D. candidate at the Technical University of Hamburg in Germany). The KUKA scenario asked us to imagine a large, automatized warehouse in which self-driving robotic carts need to pick up boxes at one point and drop them off at another location. The robots must avoid colliding with both each other and other objects. Because the boxes are elevated, the robots can drive underneath them when they are not carrying one (if they are carrying a box, however, then the two boxes would bump into each other). The robots are also usually constrained to only move along certain paths. These types of problems—known as multi-agent pickup and delivery problems in the literature—are especially difficult due to the exponential scaling of their complexity with the number of boxes, robots, and possible paths. Typically, finding even an “okay-ish” solution is a significant achievement.
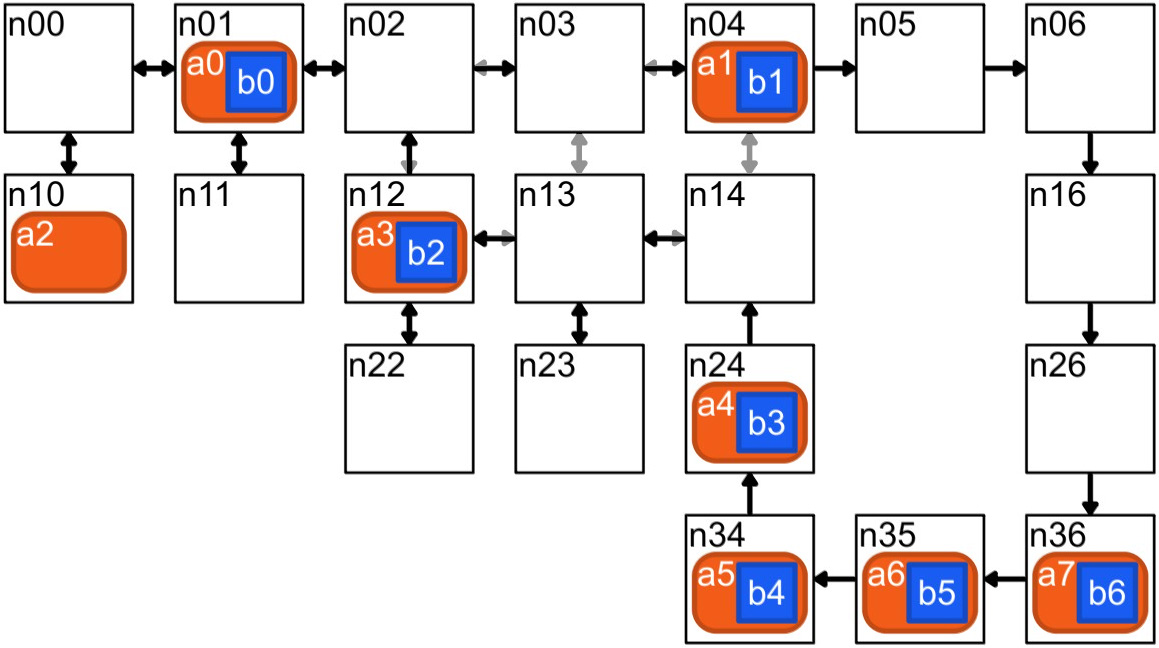
KUKA provided participating teams with code to visualize both the warehouse and the movement of the robots and boxes inside it. They also supplied a small set of examples that characterized difficult applications. In one example called the swap problem, two robots start on opposite ends of a hallway and have to pass each other to take their boxes to the other side (see Animation 1). Since the robots are blocking each other’s paths, they must work together. The optimal solution allows one robot to move out of the way so the other can pass. For a simple setup, one can easily determine whether a robot has to move out of the way and where it should go. However, this discernment is no longer possible in larger, more complex situations (see Figure 1).
Our solution strategy is inspired by the modern roundabout that is omnipresent in the Netherlands. Instead of addressing the full situation in one go, we identify highways and roundabouts to divide the large problem into smaller pieces. The robots on the roundabouts have the right of way and can move freely to their respective offramps. We can then solve each optimization problem from the offramp to the destination. For instance, a roundabout exists in Figure 1 via the grid point \(\textrm{n02} \to \textrm{n06} \to \textrm{n36} \to \textrm{n34} \to \textrm{n14} \to \textrm{n12} \to \textrm{n02}\). We enforce this traffic rule for the robots by removing certain travel directions (shown with gray arrows); doing so reduces the problem to a collection of smaller subproblems. The offramps \((\textrm{n13}, \ \textrm{n23}) \) and \((\textrm{n12}, \ \textrm{n22})\) yield almost trivial instances, and the offramp \((\textrm{n00}, \ \textrm{n01}, \ \textrm{n10}, \ \textrm{n11}, \ \textrm{n02})\) yields instances that are similar to the aforementioned swap example. This strategy earned us the top prize at the hackathon.
In conclusion, the first-ever SIAM Hackathon marked a significant milestone by uniting mathematicians from around the world to tackle real-world industry challenges from leading companies. The event showcased the ingenuity and problem-solving skills of the participants, fostered valuable connections between academia and industry, and facilitated innovative thinking at the forefront of scientific research. By hosting this unique event, SIAM created new avenues for collaboration and knowledge exchange — ultimately paving the way for future advancements at the intersection of mathematics, computation, and real-world applications.
About the Author
Tjeerd Jan Heeringa
Ph.D. candidate, University of Twente in the Netherlands
Tjeerd Jan Heeringa is a Ph.D. candidate in the Department of Applied Mathematics at the University of Twente in the Netherlands. He holds master’s degrees from the University of Twente in applied mathematics, technical computer science, and control theory.
Stay Up-to-Date with Email Alerts
Sign up for our monthly newsletter and emails about other topics of your choosing.